The research activities within the MITEC group are divided into several themes:
Measurement of the complex dielectric permittivity of materials.
Knowledge of the electromagnetic properties of materials is required in many fields of application. The MITEC group is developing characterisation techniques adapted to a wide range of materials (solids, liquids, thin films, bio-sourced materials....). A few examples are given below.
Waveguide measurement
There are numerous methods for characterising dielectric materials in the centimetre and millimetre wavelength range. These vary in terms of their measurement frequency, the size and nature of the sample (solid, liquid, gas), the level of dielectric losses in the sample, the destructive or non-destructive nature of the measurement technique, the contact or non-contact aspect of the measurement and the temperature range. The split-guide technique is one of the methods we use. The permittivity is then extracted from the S parameters measured in transmission and reflection using an inversion model. Simulation studies using the HFSS software are also carried out in support.
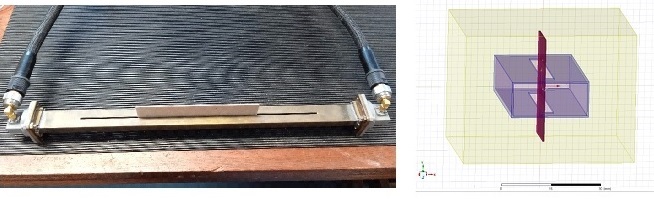
Exemple de caractérisation dans la bande 8-12 GHz & Simulation HFSS
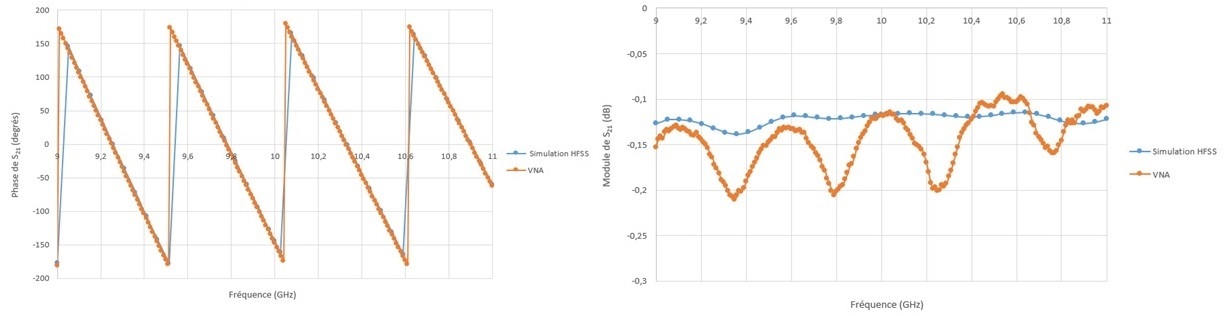
Comparaison théorie/expérience pour S21 pour un guide d’ondes fonctionnant en bande X et une fente de 2.6 mm Comparaison effectuée pour un échantillon de téflon (142mm x 32mm x 0.5mm).
Measurement using coplanar lines
For this method, the measured quantities are the parameters of the [S] matrix of CPW lines. These measurements are made using a vector analyser, connected to a sub-peak measurement station. The measurements of the [S] parameters then allow us to calculate the complex propagation constant γ = α +jβ for the lines made, where α is the attenuation constant (Np/m) and β the phase constant (Rad/m). The calculation of γ requires the measurement of the parameters [S] for two transmission lines with the same transverse dimensions (and therefore the same characteristic impedance) but different lengths.
Example: Dielectric characterisation of cellulose laurate.
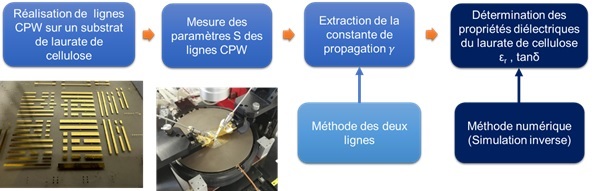
Synoptic of the method, example of lines made, measurements under spikes
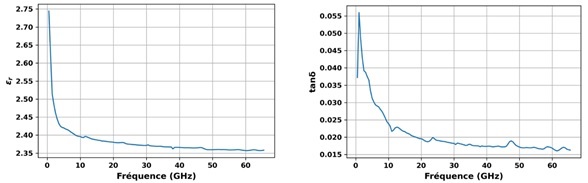
Results obtained for cellulose laurate
Measurement of the thermal conductivity of materials.
The 3ω method, which appeared in the 1990s, is an electro-thermal method for measuring the thermal conductivity of substrates or thin films deposited on substrates. A metallic thermoresistive element is deposited on the surface of the sample and a harmonic current (ω) is applied. The Joule effect, in I² induces a local rise in the temperature of the metallic element at the frequency 2ω.
The resistivity of the metal used is linked to temperature (coefficient a of the order of 10-3K-1), the measured voltage contains a component modulated at frequency 3ω. This component, amplified and measured by synchronous detection, makes it possible to determine the temperature rise of this element, which is inversely proportional to the thermal conductivity of the substrate.
- To build a 3-Omega measurement bench, it is necessary to assemble various components such as a synchronous detection amplifier, micro-positioners, a micro-ohmmeter and a current generator. A differential amplifier-based acquisition card was also manufactured. This picks up the signals present on the metal line and sends them to the inputs of the synchronous detection amplifier.
- The thermal conductivity values are obtained using inverse simulation methods developed in MATLAB© (analytical methods) or COMSOL© (numerical methods).
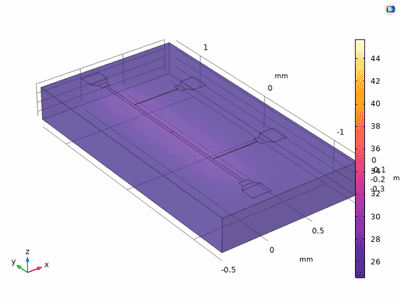
Example of temperature oscillations obtained for a line deposited on a biosourced polymer.
RF devices on flexible substrates.
Many applications are developing around wireless communications, particularly for the IoT. It is therefore necessary to develop solutions capable of adapting to new constraints, such as flexibility and energy efficiency. The MITEC group is developing devices on flexible substrates in response to these issues. Particular attention is also paid to developing devices with low environmental impact.
Production of a flexible bandpass filter at 2.45 GHz on cellulose laurate
Production of a flexible dual-band antenna on cellulose laurate for WBAN applications.
Making a rectenna on cellulose laurate