Insect vibrations inspire science
Among flying species observed in nature, insects certainly have the most impressive aerial capabilities in terms of hovering or acceleration, and remain unrivalled on these scales in terms of weight, size and energy efficiency. While understanding their flight mechanisms has long been elusive, we now know that the key to such performance lies mainly in the specific movements obtained thanks to their flexible wings, as well as the unsteady aerodynamic forces generated. A bio-inspired approach therefore appears to be a promising way of designing flying nano-robots.
The aim of the project entitled « nano-robot based on vibrating wing control » (NANOFLY) falls into this category, since it involves creating an insect-sized object, powered by electrical wires, capable of taking off and hovering.
Video 1: Wing actuation
Video 2: Lifting a nano-robot attached to a rigid beam
Initial developments have already led to some major breakthroughs: the NANOFLY team was the first to use microsystems technologies [1] to manufacture the skeleton of a nanobot with a wingspan of 25 mm. Its design is directly inspired by the order of Diptera, and consists of a support, a mobile part – a tergum and two wings – and a fixed part – the thorax (Fig. 1). The use of optical photolithography and etching processes offers the advantage of being rapid and reproducible, and has led to the production of a skeleton in SU-8 polymer resin with thicknesses ranging from 0.4 mm to 0.3 mm, as well as membranes for the wings in Parylene material and thicknesses equal to 400nm. Just as insects use their muscles to vibrate their thorax and drive their wings at several hundred beats per second, we decided to work with an entirely resonant system, without joints, excited by an electromagnetic actuator and with flexible wings to amplify the movement. In addition, our originality lies in the use of a principle combining two vibratory modes of bending and twisting the wings in phase quadrature [2], to reproduce the appropriate kinematics. Initial tests have demonstrated that a lift force equivalent to the weight of the prototype (22mg) can be obtained, with values of 30° and 15° respectively for the flapping and tilting angles of the wings (Fig.2).
The current challenges concern the take-off of the nano-robot [3]: firstly, the aim is to better understand the effects of aeroelastic couplings in order to obtain a lift force 3 times greater than the weight of the prototypes. Increasing this lift force is essential if the nano-robot is to be able to take off carrying a payload. The second challenge is to stabilize the nano-robot in hovering flight for a minimum of 10 s, which means reinforcing the flight control system and implementing the electronic functions needed for remote control. The third challenge concerns scientific and technological monitoring, with a view to ensuring the nano-robot’s eventual autonomy and use for reconnaissance missions. This involves analyzing current and future solutions for miniaturizing and lightening the existing electronic board, as well as identifying the appropriate payload and energy sources, choosing low-mass components and sensors requiring very few energy resources. We will be looking in particular at hybrid electronic circuits, CMOS micro-cameras and super-capacitors.
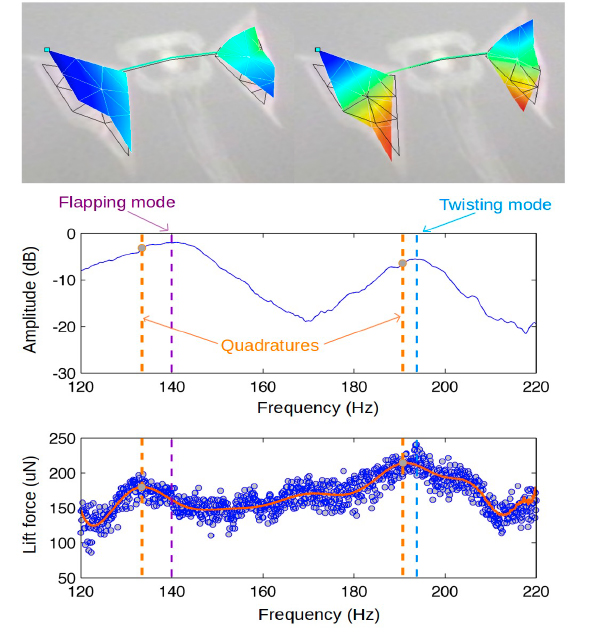
Fig. 2. a) Experimental deformations at resonance: bending and twisting modes, b) Frequency Response Function of the prototype taken at the left wing tip of the leading edge, zoomed in on the frequency range of interest. c) Average lift force for several excitation frequencies with polynomial curve fitting.
References :
[1] Bao, X. Q., et al. « Design and fabrication of insect-inspired composite wings for MAV application using MEMS technology. » Journal of Micromechanics and Microengineering 21.12 (2011): 125020.
[2] Faux, D., Thomas, O., Cattan, E., & Grondel, S. (2018). Two modes resonant combined motion for insect wings kinematics reproduction and lift generation. Europhysics Letters, 121(6), 66001.
[3] Grondel, Sébastien, et al. « Towards the use of flapping wing nano aerial vehicles. » Modern Technologies Enabling Safe and Secure UAV Operation in Urban Airspace 59 (2021): 52.
Dissemination to the general public:
1. E. Cattan
Le plus petit drone du monde présenté à Valenciennes, Journal Télévisé France 3, 19/20 Nord Pas-de-Calais, 10 octobre 2023
https://france3-regions.francetvinfo.fr/archives/2023/10-octobre-2023
2. E. Cattan, S. Grondel, Quand la nature inspire l’innovation, Exposition à l’IMTD, 10 octobre 2023
https://imtd.fr/evenements/expo-nature-inspire-innovation/
3. S. Grondel, E. Cattan, Ces chercheurs qui se sont mis en tête de faire voler un drone de la taille d’une mouche, La Voix du Nord, 4 octobre 2023
https://www.lavoixdunord.fr/1381005/article/2023-10-04/ces-chercheurs-qui-se-sont-mis-en-tete-de-faire-voler-un-drone-de-la-taille-d
4. S. Grondel, H. Poirier, Du microrobot au nanorobot, France Culture, Continent sciences, 30 mai 2016
https://www.radiofrance.fr/franceculture/podcasts/continent-sciences/du-microrobot-au-nanorobot-2637360
5. S. Grondel, Le robot-abeille, Science & Vie, n°1185, 58-59, juin 2016,
https://www.science-et-vie.com/article-magazine/robot-abeille-ses-ailes-vibrantes-reinventent-le-vol